Institutul francez de energie solară INES a dezvoltat noi module fotovoltaice cu termoplastice și fibre naturale provenite din Europa, cum ar fi inul și bazaltul.Oamenii de știință își propun să reducă amprenta asupra mediului și greutatea panourilor solare, îmbunătățind în același timp reciclarea.
Un panou din sticlă reciclată în față și un compozit de in pe spate
Imagine: GD
De la pv magazine France
Cercetătorii de la Institutul Național de Energie Solară (INES) din Franța – o divizie a Comisiei pentru Energii Alternative și Energie Atomică (CEA) din Franța – dezvoltă module solare care includ noi materiale pe bază de bio în partea din față și din spate.
„Deoarece amprenta de carbon și analiza ciclului de viață au devenit acum criterii esențiale în alegerea panourilor fotovoltaice, aprovizionarea cu materiale va deveni un element crucial în Europa în următorii câțiva ani”, a declarat Anis Fouini, directorul CEA-INES. , într-un interviu acordat revistei pv France.
Aude Derrier, coordonatorul proiectului de cercetare, a declarat că colegii ei s-au uitat la diferitele materiale care există deja, pentru a găsi unul care ar putea permite producătorilor de module să producă panouri care îmbunătățesc performanța, durabilitatea și costul, reducând în același timp impactul asupra mediului.Primul demonstrator constă din celule solare cu heterojoncție (HTJ) integrate într-un material complet compozit.
„Partea frontală este realizată dintr-un polimer umplut cu fibră de sticlă, care oferă transparență”, a spus Derrier.„Partea din spate este realizată din compozit pe bază de termoplastice în care a fost integrată o țesătură din două fibre, in și bazalt, care va oferi rezistență mecanică, dar și o mai bună rezistență la umiditate.”
Inul provine din nordul Franței, unde întregul ecosistem industrial este deja prezent.Bazaltul provine din altă parte din Europa și este țesut de un partener industrial al INES.Acest lucru a redus amprenta de carbon cu 75 de grame de CO2 per watt, comparativ cu un modul de referință de aceeași putere.Greutatea a fost și ea optimizată și este mai mică de 5 kilograme pe metru pătrat.
„Acest modul are ca scop integrarea PV pe acoperiș și clădire”, a spus Derrier.„Avantajul este că este în mod natural de culoare neagră, fără a fi nevoie de o foaie de spate.În ceea ce privește reciclarea, datorită materialelor termoplastice, care pot fi topite, separarea straturilor este, de asemenea, mai simplă din punct de vedere tehnic.”
Modulul poate fi realizat fără adaptarea proceselor curente.Derrier a spus că ideea este de a transfera tehnologia producătorilor, fără investiții suplimentare.
„Singurul imperativ este de a avea congelatoare pentru a stoca materialul și nu pentru a începe procesul de reticulare a rășinii, dar majoritatea producătorilor de astăzi folosesc preimpregnat și sunt deja echipați pentru acest lucru”, a spus ea.
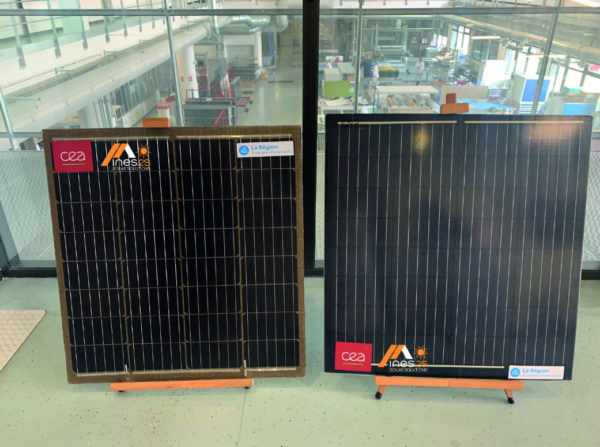
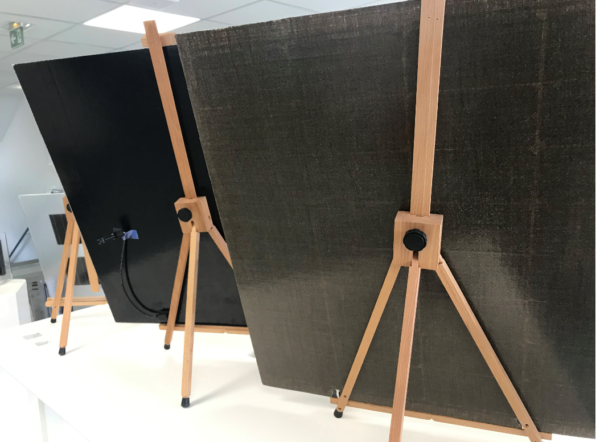
„Am lucrat la a doua durată de viață a sticlei și am dezvoltat un modul format din sticlă reutilizată de 2,8 mm care provine dintr-un modul vechi”, a spus Derrier.„Am folosit, de asemenea, un încapsulant termoplastic care nu necesită reticulare, care va fi, prin urmare, ușor de reciclat, și un compozit termoplastic cu fibră de in pentru rezistență.”
Fața din spate fără bazalt a modulului are o culoare naturală de in, care ar putea fi interesantă din punct de vedere estetic pentru arhitecți în ceea ce privește integrarea fațadei, de exemplu.În plus, instrumentul de calcul INES a arătat o reducere cu 10% a amprentei de carbon.
„Acum este imperativ să punem sub semnul întrebării lanțurile de aprovizionare fotovoltaice”, a spus Jouini.„Cu ajutorul regiunii Rhône-Alpes în cadrul Planului Internațional de Dezvoltare, am căutat, prin urmare, jucători din afara sectorului solar pentru a găsi noi termoplastice și noi fibre.Ne-am gândit și la procesul actual de laminare, care consumă foarte mult energie.”
Între faza de presurizare, presare și răcire, laminarea durează de obicei între 30 și 35 de minute, cu o temperatură de funcționare de aproximativ 150 C până la 160 C.
„Dar pentru modulele care încorporează din ce în ce mai mult materiale eco-proiectate, este necesară transformarea materialelor termoplastice la aproximativ 200 C până la 250 C, știind că tehnologia HTJ este sensibilă la căldură și nu trebuie să depășească 200 C”, a spus Derrier.
Institutul de cercetare face echipă cu specialistul în termocompresie prin inducție Roctool din Franța, pentru a reduce timpii de ciclu și a realiza forme în funcție de nevoile clienților.Împreună, au dezvoltat un modul cu o față posterioară din compozit termoplastic de tip polipropilenă, în care au fost integrate fibre de carbon reciclate.Partea frontală este realizată din termoplastic și fibră de sticlă.
„Procesul de termocompresie prin inducție Roctool face posibilă încălzirea rapidă a celor două plăci din față și din spate, fără a fi nevoie să se atingă 200 C la miezul celulelor HTJ”, a spus Derrier.
Compania susține că investiția este mai mică și că procesul ar putea atinge un timp de ciclu de doar câteva minute, folosind mai puțină energie.Tehnologia se adresează producătorilor de compozite, pentru a le oferi posibilitatea de a produce piese de diferite forme și dimensiuni, integrând în același timp materiale mai ușoare și mai durabile.
Ora postării: 24-jun-2022